Introduction to 3D Printing Materials
3D printing, also known as additive manufacturing, has revolutionized the field of fabrication, allowing for the creation of complex, custom objects with unprecedented ease. Central to the success of 3D printing is the diversity of materials available for use—a variety that continues to expand as the technology progresses. These materials can broadly be categorized into thermoplastics, resins, and several advanced composites. Understanding the unique properties of these materials is crucial in optimizing print quality and functionality for specific applications.
Thermoplastics are among the most commonly used 3D printing materials. They include popular options like Polylactic Acid (PLA) and Acrylonitrile Butadiene Styrene (ABS). PLA is known for its ease of use, biodegradability, and a relatively low melting point, making it ideal for beginners and educational purposes. ABS, on the other hand, offers greater strength and durability, albeit with a higher melting point and a need for more advanced printing conditions. These properties determine the best use-cases for each type of thermoplastic, impacting factors such as mechanical strength, flexibility, and thermal resistance.

Beyond thermoplastics, resins provide another dimension to 3D printing, primarily used in SLA (Stereolithography) and DLP (Digital Light Processing) printers. Resins are known for producing high-detail prints with smooth finishes, making them ideal for intricate designs and professional applications. However, they typically require post-processing involving curing and washing, adding another layer of complexity to the printing process. As with thermoplastics, the choice of resin depends on the specific requirements of the project, including desired finish, strength, and durability.
The evolution of 3D printing materials dates back to the 1980s when the first 3D printers primarily used a limited range of polymers. Over time, the variety has grown to include advanced composites, metals, and even biocompatible materials. This expansion has opened new opportunities across various sectors, from prototyping and manufacturing to medical and aerospace applications. Selecting the appropriate material not only enhances print quality and performance but also ensures the success of the project at hand.
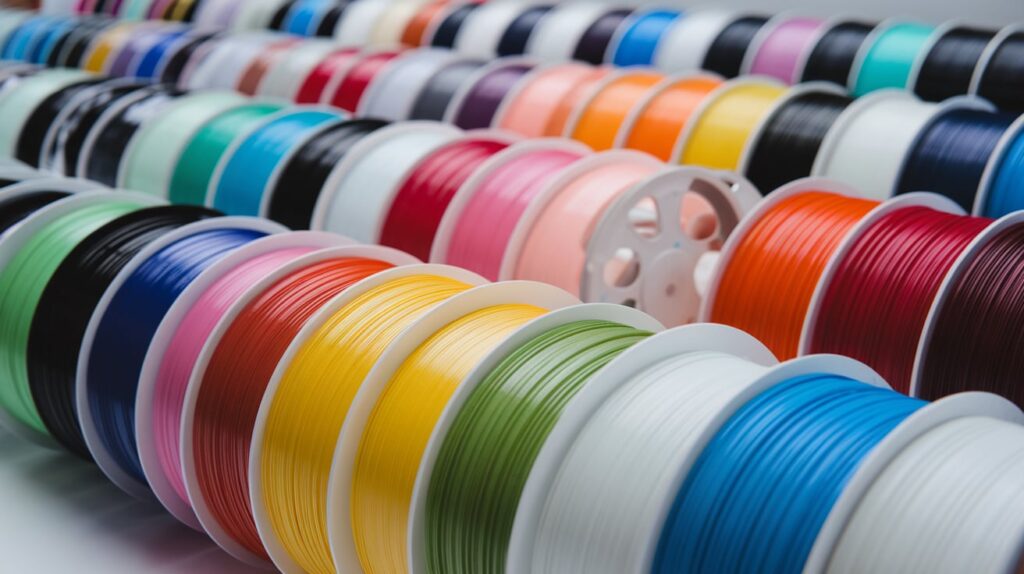
PLA: Polylactic Acid
Polylactic Acid (PLA) is a popular 3D printing material lauded for its environmental friendliness. Composed of renewable resources such as corn starch or sugarcane, PLA is biodegradable, making it an eco-conscious choice for various 3D printing applications. Its user-friendly properties and low cost make it particularly attractive to beginners in the 3D printing arena.
One of the standout features of PLA is its relatively low melting temperature, which typically ranges between 180-220°C. This lower melting point facilitates smoother and quicker printing processes, reducing the chances of warping and making it easier to handle compared to other materials like ABS. PLA’s tensile strength is appreciable, generally falling between 37-60 MPa, which is sufficient for most non-load-bearing applications. Furthermore, PLA is biocompatible, meaning it can safely be used for items that come into contact with the human body, such as customized prosthetics or dental models.

The applications of PLA are diverse, ranging from prototyping and educational models to decorative items and simple functional parts. Its rigid structure and ease of use make it suitable for creating intricate designs and detailed models. PLA is also widely used to produce art pieces, miniature models, and even household items, thus showcasing its versatility.
However, PLA has its limitations. Its susceptibility to heat is a significant drawback; PLA can lose its structural integrity at temperatures above 60°C, making it unsuitable for high-heat applications. Additionally, while PLA offers decent durability, it is generally less robust compared to materials like ABS or Nylon. This lower durability means that PLA-printed objects are more prone to cracking or breaking under stress and are not ideal for high-impact applications.
In summary, PLA’s ease of use, affordability, and eco-friendliness make it a fantastic choice for both novice and experienced 3D printing enthusiasts, despite its limitations concerning heat resistance and durability.

ABS: Acrylonitrile Butadiene Styrene
Acrylonitrile Butadiene Styrene (ABS) is a thermoplastic polymer widely regarded for its superior durability and heat resistance compared to other common 3D printing materials such as PLA. The composition of ABS includes acrylonitrile, butadiene, and styrene, which collectively confer mechanical strength, malleability, and enhanced toughness to the material. This makes ABS particularly suitable for high-stress applications and industrial purposes.
ABS is commonly utilized in the production of automotive parts, electronic enclosures, and even everyday items like Lego bricks. Its robust nature allows it to withstand mechanical stress and temperatures that would deform or compromise other materials. The mechanical properties of ABS include high tensile strength, excellent impact resistance, and good dimensional stability. These attributes make it a preferred choice for functional prototypes and end-use parts that need to endure rough handling and fluctuating temperatures.

However, printing with ABS comes with its own set of challenges. Foremost is its requirement for a higher printing temperature, typically in the range of 220-250°C. Additionally, ABS has a tendency to warp as it cools, which necessitates the use of a heated bed to maintain consistent temperature throughout the build process. Warping can be mitigated further by employing an enclosed and well-ventilated printing environment to control ambient conditions.
When compared to PLA, ABS showcases superior toughness and heat resistance, making it more suited for products that will face cyclical loads and exposure to heat. However, it is less user-friendly than PLA due to its higher emission of fumes during printing, which underscores the need for good ventilation. Despite the demanding operational requirements, ABS remains a top choice for applications where strength, durability, and heat resistance are paramount. As such, scenarios that demand mechanical robustness and thermal durability repeatedly see ABS outperforming other commonly used 3D printing materials.
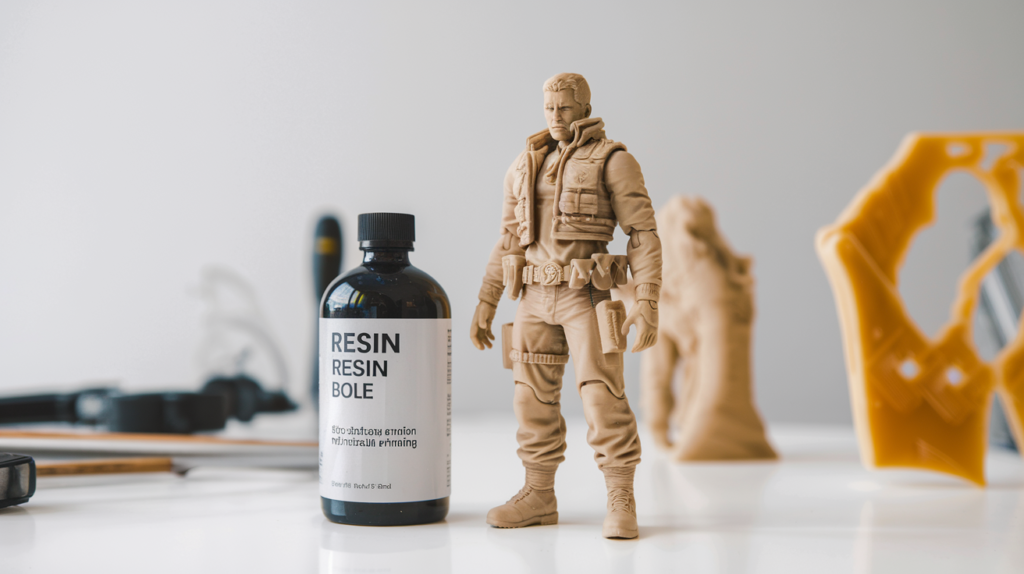
Resin: Photopolymer and UV Resin
Resin materials are predominantly used in SLA (Stereolithography) and DLP (Digital Light Processing) 3D printing technologies. The key component of these resins is the photopolymer, a chemical compound that undergoes polymerization when exposed to ultraviolet (UV) light. This curing process transforms the liquid resin into a solid, highly precise, and durable material, making it ideal for applications demanding fine detail and a smooth surface finish.

Photopolymer resins come in a variety of formulations tailored for specific applications. Standard resins are commonly used for general-purpose prototyping and produce models with excellent detail and smooth surfaces. Flexible resins offer unique properties such as rubber-like elasticity, making them perfect for creating components that require flexibility and impact resistance. Tough resins are engineered to mimic the durability and strength of ABS plastics, providing high-performance parts suitable for functional prototypes and mechanical assemblies. Meanwhile, bio-compatible resins are specially formulated to meet stringent regulatory standards, making them suitable for medical and dental applications such as surgical guides and dental models.
Industries such as dentistry, jewelry, and miniatures heavily rely on the precision and high quality of resin-based printing. In dentistry, resins are used to create accurate dental models, crowns, and bridges. Jewelry makers take advantage of the fine detail and smooth surface finish to produce intricate designs and casting molds. Similarly, hobbyists and professional model makers use resin for producing detailed miniatures and functional prototypes.
Despite their advantages, working with resin requires strict handling and safety precautions. Uncured resins are typically toxic and can cause skin irritation or allergic reactions. It is essential to wear gloves, masks, and protective eyewear when handling uncured resin, and ensure proper ventilation in the working area. Additionally, disposal of resin waste must comply with local environmental regulations to prevent ecological damage.
In terms of benefits, resin-based materials excel in providing superior detail and surface quality compared to filament-based materials like PLA and ABS. However, they can be more expensive and require meticulous post-processing for curing and cleaning. Understanding these nuances helps industry professionals and enthusiasts alike to choose the appropriate material for their specific needs.